A laid-over pleat geometry which offers improved performance and a reduction in filtration operating costs.
- Longer filter element service life
- Up to 50% smaller and lighter
- OEM approved
Why do Ultipleat elements have lower operating costs?
Long Service LifeThe unique, laid-over pleat geometry provides a greater filtration area than conventional ‘fan-pleat’ filter elements for the same envelope. This, coupled with a more uniform flow distribution results in a significant increase in dirt holding capacity when compared to a fan (radial) pleat construction in the same space envelope.
Side by side comparison testing has shown
Up to 50% more dirt capacity for Ultipleat compared to conventional fan pleat
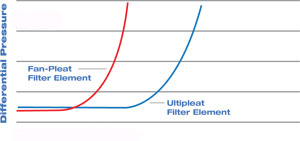
Alternatively, the larger filtration area can be used to design an Ultipleat filter element with a finer micron rating and the same service life compared to a fan-pleat design in the same space envelope.
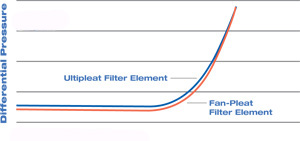
Low weight and space requirements
Ultipleat elements have a lower flow density, and consequently, a higher flow capacity. As a result, filter size can be reduced substantially. The smaller size combined with polymeric support meshes reduces weight by as much as 50%.
The higher dirt capacity(service life) for the same envelope can be traded off for a smaller envelope with the same dirt capacity as the conventional radial pleat filter element. In addition, the use of polymeric support meshes can also lead to a substantial reduction in filter element weight.
A low average pressure drop is important for keeping energy consumption to a minimum. This allows more flow through the filter during low temperature, high viscosity start-up conditions.
Stability of performanceThe pleats are supported both upstream and downstream which helps to maintain efficiency and performance during cyclic flow or cyclic pressure(pump ripple) conditions.
Why do Ultipleat elements have a uniform flow distribution?
![]() |
![]() |
|
Conventional pleated filter element construction, showing Non-uniform flow distribution (Outside to Inside flow direction).In a conventional filter element the pleats radiate outward from the core and the spacing between the pleats increases. This space represents wasted volume and unused filtration area. |
Ultipleat filter element construction showing uniform flow distribution (Outside to Inside flow direction).
|
Why do some engines use a reverse-flow filter element?
In a reverse-flow Ultipleat design, the fluid flows from Inside to Outside and all the contaminants are retained inside the filter element. This concept offers several benefits:
- Weight saving - structural core can be integrated into the filter bowl
- Simpler maintenance - no need to clean filter bowl
- Less chance of cross-contamination during filter element change out
- Engine Lube
- Engine Fuel
- Hydraulic
- Helicopter Transmissions
- Liquid Cooling
Literature and Other Resources
Aerospace Ultipleat Data sheet
Optimizing Filter Element Design for Size, Weight and Life Improvements, Paper No. IFC10-002
Our filter elements are designed and tailored to meet the customer specification requirements.
If you have an aerospace application that needs an Ultipleat laid-over pleat design, please talk to one of our experts Contact Aerospace
For commercial aircraft products, please contact our authorised distributor, Satair
Earn 10% off* your next order online by leaving a review of this product. Please login to your account to leave a review. We appreciate and value your feedback.
*Subject to Terms and Conditions.