For Yeast Management
The increasing cost of raw materials and energy are forcing the brewing industry to investigate new opportunities for increasing extract yield without compromising quality. Excess yeast contains a significant amount of extract which can be recovered by concentrating the yeast with modern cross flow technology. By combining this technology with controlled diafiltration the yield can even be boosted. The recovered beer can be blended to the original beer up to a level of 5% volume without negatively influencing the taste. Thus, beer recovery can make a big contribution to cost savings in the brewery.Benefits
- Cost reduction can include
- Very short return on investment (ROI) of about 1 year
- Net revenue > 90% of the invested capital per year
- High mechanical, thermal and chemical resistance of membranes for longer module lifetime
- Easy installation due to modular concept
- High system availability
- Dry matter up to 20% for high yield
- Low maintenance cost
- Low operating expense (OPEX)
- High quality yeast for sale
- Excellent beer quality
- Minimal difference between original beer and blended beer in terms of sensory and analytics
- Closed system for minimum oxygen uptake
- Clear cut off with low turbidity and almost yeast free beer
- High microbiological safety due to easy cleaning and sterilization with hot water up to
90 °C (194 °F) - Easy to extend due to modular concept
- High yield, long module lifetime, consistent beer quality and reduced energy consumption due to controlled process
Diafiltration Principle
In this special process developed by Pall, water is added to the yeast suspension to increase the extract and alcohol recovery (wash out effect) without compromising the beer quality.Filter Media
Membralox® Ceramic Membranes
- High flux
- Proven long operational life
- Excellent resistance to corrosion
- Wide chemical and pH (0 - 14) compatibility
- Excellent thermal stability
- Can be sanitized and sterilized
Membralox Modules
- High performance housing design and sealing assembly
- Membralox SD and HCB modules
Analytical Results and Taste Panel Data
To evaluate the percentage of beer which can be blended back to production without compromising the beer quality, several test were conducted. By chemical and sensory analysis carried out by independent institutes, it was shown that a back blending ratio of up to 5 % volume is suitable. The superior quality of the recovered and blended beers has been confirmed as follows:- No identification of blended beers by taste panel
- Minimum deviation (within analytical method sensitivity) by basic analytics
- No significant differences on esters
- No significant differences on short chain fatty acids
- No significant difference in stale flavor active substances
Commercial Aspects
The short ROI with a range between 1 - 2 years make this technology and the investment made into it very attractive to the brewing industry.Example
Brewery A | Brewery B | |
Beer output (12° Plato)* | 4,000,000 hl/a | 2,000,000 hl/a |
Brew house output (16° Plato)* | 3,000,000 hl/a | 1,500,000 hl/a |
Yeast amount (16° Plato, 3% of brew house output)* | 90,000 hl/a | 45,000 hl/a |
Recovered beer (~ 80 % yield; 10.5° Plato) | 110,000 hl/a | 50,000 hl/a |
Beer production cost (at 10 €hl)* | 1,100,000 € | 500,000 € |
Investment for system* | 500,000 € | 400,000 € |
Investment for periphery* | 500,000 € | 500,000 € |
OPEX* / hl | 0.33 € | 0.40 € |
OPEX / annum | 36,300 € | 20,000 € |
Costs (CAPEX + OPEX) | 1,036,300 € | 920,000 € |
Gain / annum | 1,100,000 € | 500,000 € |
Return on investment 1 - 2 years |
||
*Estimation
Technical data
Keraflux-TFF System | ||||||||
Module lines x modules high | 2 x 2 SD | 2 x 3 SD | 2 x 2 HCB | 2 x 3 HCB | 3 x 2 HCB | 3 x 3 HCB | 3 x 4 HCB | |
Brewery size1 [hl/a] | 2000,000 | 3300,000 | 3300,000 | 4800,000 | 4800,000 | 7300,000 | 9700,000 | |
Yeast amount2 [hl/day] | 190 | 310 | 310 | 460 | 460 | 700 | 930 | |
Footprint filtration unit [m] | Length | 4.50 | 4.50 | 4.50 | 4.50 | 5.50 | 5.50 | 5.50 |
Width | 2.00 | 2.00 | 2.00 | 2.00 | 2.00 | 2.00 | 2.00 | |
Height | 4.50 | 5.50 | 4.50 | 5.50 | 4.50 | 5.50 | 6.70 | |
Footprint service unit [m] | Length | 2.55 | 2.55 | 2.55 | 2.55 | 2.55 | 2.55 | 2.55 |
Width | 2.25 | 2.25 | 2.25 | 2.25 | 2.25 | 2.25 | 2.25 | |
Height | 2.00 | 2.00 | 2.00 | 2.00 | 2.00 | 2.00 | 2.00 | |
112° Plato
2Yeast amount: 3% of beer volume (12 ° Plato)
15° Plato
250 working days per year
21 h filtration per day
Cost Reduction by Process Control
The process for yeast extract recovery uses a ceramic cross flow technology with specific control features to achieve reduced costs.- Cost savings
- low consumption of cleaning agents and water
- high system availability and production time
- Long production cycles and less cleaning cycles
- Control of feed flow
- Control of cross flow velocity
- Control of permeate flow and trans membrane pressure (TMP) at each module level against target set points
Process Description
The beer recovery is conducted in a batch process, which offers several advantages:- Improved performance (up to 20%) and quality due to lower yeast concentration in system during batch cycle
- Reduced energy consumption (up to 25%) due to lower yeast concentration in system during batch cycle
- Yield up to 80% due to diafiltration
Keraflux-TFF System 2 x 3
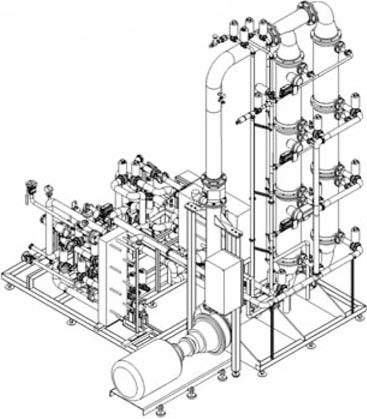
TFF Systems
Tangential Flow Filtration
Earn 10% off* your next order online by leaving a review of this product. Please login to your account to leave a review. We appreciate and value your feedback.
*Subject to Terms and Conditions.