The inability to efficiently separate liquid/liquid emulsions can be a very costly problem in the oil, gas, and chemical industries. Liquid contamination can cause final products to be off-specification, rapid deactivation of downstream catalysts, corrosion of downstream storage facilities, and increased costs for wastewater treatment.
Separating liquid/liquid dispersions can be difficult depending on the physical properties of the two liquid phases. The specific gravity, viscosity, and interfacial tension (IFT) of the two liquid phases are important parameters in determining how easy two liquids can be separated. Conventional coalescers begin to lose efficiency when the IFT gets below 20 dyne/cm. In addition, efficient separation is a function of the compatibility of the liquids with the coalescer medium. A good coalescing medium is not necessarily compatible with the liquids and a compatible medium is not necessarily a good coalescing medium.
Description
A Pall PhaseSep system is available in two different configurations. Both configurations begin with a filtration stage to remove solid contaminants.
Prefiltration
Due to the fine pore structure of the coalescer medium, Pall recommends that a prefilter be installed upstream of the coalescer assembly. Removal of solids performs the following important functions:
- Extends the life of the coalescer significantly.
- Reduces particulate concentration meeting fluid specifications.
- Decreases stability of the liquid/liquid emulsion, thereby making liquid/liquid separation easier.
Two different housing configurations are available for PhaseSep coalescers. Table 1 provides guidelines for selection.
Table 1: Coalescer Selection Guide
Process Condition | Recommended Product |
Dispersed phase fluid is aqueous IFT > 3 dyne/cm | PhaseSep coalescer/separator stack in a vertical housing |
Dispersed phase fluid is aqueous IFT < 3 dyne/cm | PhaseSep coalescer without separator in a horizontal housing |
Both fluids are non-aqueous | PhaseSep coalescer without separator |
Dispersed phase fluid is oil, continuous phase fluid is aqueous | PhaseSep coalescer in a horizontal housing without separator |
Benefits
- Improved Fluid Quality and Value: The superior liquid and particulate removal efficiency reduces incidents of off-spec product thereby saving reprocessing, downgrade and transportation costs. In addition, carried over liquid contaminants can cause costly corrosion problems in downstream equipment and can rapidly deactivate expensive catalysts in downstream processes.
- Low-Cost Liquid and Solids Removal: Due to the PhaseSep coalescer’s long life and superior liquid removal efficiency, the overall cost of contaminant removal is low even when compared to other less efficient methods like salt driers, electrostatic separators and sand filters. Used in conjunction with these other removal techniques, the PhaseSep system will significantly reduce operating costs.
- High-Performance Stack Design Results in Smaller Assembly Size: The high performance PhaseSep system stack design promotes even flow distribution permitting a high rate of flow. As a result, fewer separator cartridges are required and this results in a small economic assembly size.
- Lower Disposal and Maintenance Costs: The long useful life of the PhaseSep cartridges obtained from Pall’s specially formulated medium and prefilter results in fewer cartridge changeouts, reducing maintenance and changeout costs and cartridge disposal costs.
- Quick Recovery from Process Upsets: Pall’s vertical vessel/stack design is much more forgiving when it comes to changes in process conditions.
- Separation of Ultra-Low IFT Emulsions: PhaseSep coalescers have excellent coalescing properties, which can separate liquids that have ultra-low IFTs heretofore unable to be separated by conventional coalescers. With the combination of the PhaseSep coalescer and Pall’s specially designed horizontal housing, the PhaseSep system has separated liquid/liquid emulsions with an IFT greater than 0.5 dyne/cm. Conventional coalescers begin to rapidly lose separation efficiency when the IFT gets below 20 dyne/cm.
Features
- Unique Stack Design: Pall’s coalescer element is stacked on top of a separator element. This unique configuration optimizes the flow distribution from the coalescer to the separator, ensuring that each separator has an equal flow. In conventional two-stage systems, the separators are located at different distances from the coalescer, causing an unequal distribution of flow to the separator. These conventional two stage systems require several coalescer elements for each separator. Pall’s stack design results in overall smaller assembly size and a longer coalescer/separator life.
- Fluid Compatibility: Pall’s PhaseSep coalescer is available in several different materials to insure compatibility with virtually any type of liquid/liquid mixture.
- Non-Disarming Medium: Pall’s non-disarming medium ensures the longest possible service life. Pall’s specially formulated medium contains no glass fiber and does not disarm in the presence of surfactants. Disarming occurs when surfactants (either natural or additives) “coat” the surface of the medium thereby reducing the coalescing properties of the medium and the separation efficiency.
Typical Applications for PhaseSep Coalescers
- Removal of carried-over caustic from refinery fuels downstream of caustic treating processes.
- Separation of oil from water.
- Removal of water and caustic from online analyzer sampling systems.
- Separation of water from hydrogen peroxide working solutions.
- Separation of hydrogen peroxide working solutions from hydrogen peroxide.
- Removal of carried-over amine from hydrocarbon downstream of a liquid/liquid amine contactor.
- Removal of oil from ammonia.
- Separation of pyrolysis gas from quench water in ethylene plants.
The Pall PhaseSep system is a multiple stage system starting with filtration to remove particulate matter*, followed by either a one-stage or two-stage coalescer stack to separate the two liquid phases. PhaseSep coalescers will remove a liquid contaminant to a level of 15 ppmv and below over a wide range of conditions such as:
- Inlet liquid contaminant concentration as high as 10%.
- Interfacial tension greater than 0.5 dyne/cm.
*Pall recommends using Pall Ultipleat® High Flow filters with Ultipor® GF medium (10µm = 5000) or Pall filters with Epocel® medium (10µm = 5000) as a prefilter to extend the life of the PhaseSep coalescer. Consult a Pall distributor to determine compatibility with a specific fluid.
Pall’s PhaseSep coalescer/separator stack should be used when the contaminant is an aqueous liquid such as water, caustic, or an amine solution and when the IFT is greater than 3.0 dyne/cm. (see Figure 1). Using Pall’s coalescer/ separator stack in Pall’s unique vertical housing design is the most efficient technique for separating two liquids meeting the above criteria. The liquid/liquid mixture enters the coalescing element and flows inside to outside. This is where small liquid droplets suspended in the continuous phase come together, or coalesce, as the mixture moves through Pall’s proprietary coalescer medium.
Contaminant-free liquid and large droplets of the dispersed phase flow toward the separator located directly below the coalescer stage. The flow is outside to inside. The separator medium is hydrophobic preventing the aqueous phase from entering the separator. Only the non-aqueous continuous phase fluid flows through the separator. The two liquids are removed by separate drain connections.
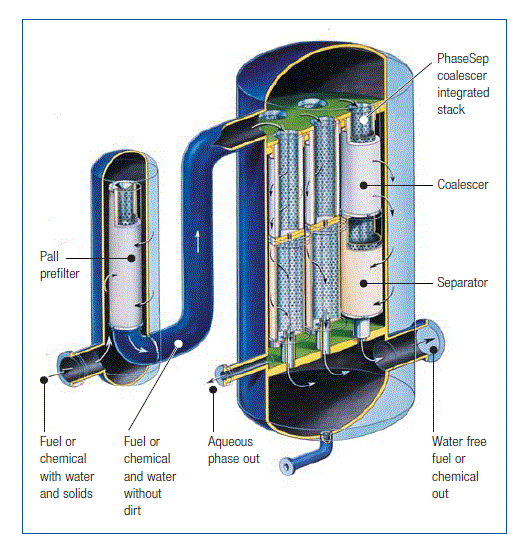
Figure 1: PhaseSep Liquid/Liquid Separation System with an Integrated Coalescer/Separator Stack in a Vertical Housing with a Prefilter
Pall PhaseSep Coalescer-Horizontal Housing Setup
In general, a PhaseSep coalescer without a separator is placed in a horizontal housing (see Figure 2). Pall’s PhaseSep coalescer should be used in applications to separate nonaqueous liquid contaminants such as removing oil from water or separating two non-aqueous liquids. In addition, for liquids with ultra-low IFTs (less than 3.0 dyne/cm.), a PhaseSep coalescer installed in a horizontal housing will provide maximum liquid/liquid separation efficiency.
In a horizontal housing, the liquid/liquid mixture enters the coalescing element and flows inside to outside. As is the case with the coalescer/separator stack, small liquid dispersed phase droplets suspended in the continuous phase come together, or coalesce, as the mixture moves through the PhaseSep coalescer. The large coalesced droplets of the dispersed phase separate by gravity in the horizontal housing and are removed. The size of the housing is a function of the IFT, viscosity, and specific gravity of the liquids.
Figure 2: PhaseSep Liquid/Liquid Separation System with Coalescer in a Horizontal Housing with a Prefilter.
Maximum Operating Temperature: | 149°C/300°F |
Initial Pressure Drop: | 0.138 bard/2 psid |
Recommended Changeout: | 1.033 bard/15 psid |
The ‘original’ PhaseSep® Coalescer—often used for caustic/hydrocarbon and Pygas/quench water separations2
Part Number | Description | Length (cm/ in) | O-Ring |
LCS2H1AH Variants: |
PhaseSep Coalescer | 50.8/20 | Fluoropolymer |
LCS2H1AH1 | PhaseSep Coalescer | 50.8/20 | Fluoropolymer Encapsulated Teflon3 |
LCS2H1AH11 | PhaseSep Coalescer | 50.8/20 | Teflon4 |
LCS4H1AH Variants: |
PhaseSep Coalescer | 101.6/40 | Fluoropolymer |
LCS4H1AH1 | PhaseSep Coalescer | 101.6/40 | Fluoropolymer Encapsulated Teflon |
LCS4H1AH11 | PhaseSep Coalescer | 101.6/40 | Teflon |
LSS2F1H | Separator | 50.8/20 | Fluoropolymer |
Polycapped PhaseSep® Coalescer—more chemically resistant than the ‘original’ PhaseSep because of fluoropolymer endcaps and no epoxy5
Part Number | Description | Length (cm/ in) | O-Ring |
LCS2H2HH Variants: |
PhaseSep Coalescer | 50.8/20 | Fluoropolymer |
LCS2H2HH1 | PhaseSep Coalescer | 50.8/20 | Fluoropolymer Encapsulated Teflon |
LCS2H2HH11 | PhaseSep Coalescer | 50.8/20 | Teflon |
LCS4H2HH Variants: |
PhaseSep Coalescer | 101.6/40 | Fluoropolymer |
LCS4H2HH1 | PhaseSep Coalescer | 101.6/40 | Fluoropolymer Encapsulated Teflon |
LCS4H2HH11 | PhaseSep Coalescer | 101.6/40 | Teflon |
LSS2F1H | Separator | 50.8/20 | Fluoropolymer |
2NOTE: The following specifications apply to all ‘original’ PhaseSep Coalescer configurations: Outer diameter = 9.53 cm/3.75 in; Media = pleated fluoropolymer;
End cap = stainless steel
3Also referred to as FEP encapsulated fluoropolymer
4Teflon is a registered trademark of The Chemours Company.
5NOTE: The following specifications apply to all ‘Polycapped’ PhaseSep Coalescer configurations: Outer diameter = 9.53 cm/3.75 in; Media = pleated fluoropolymer; End cap = polycapped fluoropolymer
Pall Part Number = LC[1][2]H[3][4][5]
Table 1
Code | Hardware |
S | 304 stainless steel |
X | Hastelloy (for special compatibility issues) |
Table 2
Code | Cartridge length (cm/ in) |
06 | 15.24 /6 |
2 | 50.8 /20 |
4 | 101.6 /40 |
Table 3
Code | Internal Use only |
1 or 2 | //////////////////////////////////////////// |
Table 4
Code | End cap material |
A | 304 stainless steel |
H | Polycapped fluoropolymer |
Table 5
Code | O-rings |
H | Fluoropolymer |
H1 | Teflon encapsulated fluoropolymer |
H11 | Teflon (FEP) |
Earn 10% off* your next order online by leaving a review of this product. Please login to your account to leave a review. We appreciate and value your feedback.
*Subject to Terms and Conditions.